HARDWARE INFORMATION
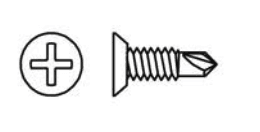
SCREW PACK 1
#10 x 3/4” Phillips Flat Head Undercut Self-Drilling Screws
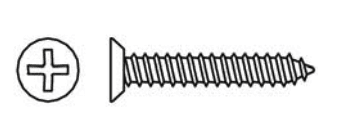
SCREW PACK 2
#10 x 1 1/4” Phillips Flat Head Undercut Sheet Metal Screws
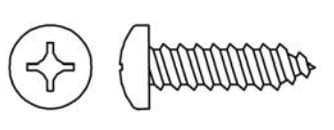
SCREW PACK 3
#14 x 1” Pan Head Wood Screw
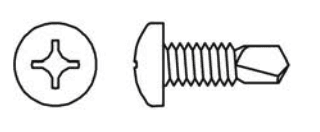
SCREW PACK 4
1/4-20 x 3/4” Phillips Pan Head Self-Drilling Tek Screws
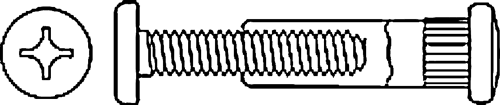
SCREW PACK 5
1/4-20 x 1-3/4” Sexbolt
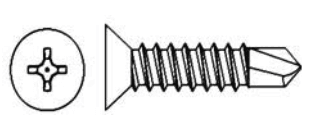
SCREW PACK 6
#8 x 3/4” Phillips Flat Head Undercut Sheet Metal Screws
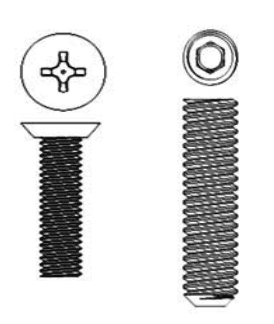
SCREW PACK 7
1-3/8” Adjustment Screw with 10-32 Internal Thread for Left Hand with 10-32 x 3/4” Flat Head Machine Screw
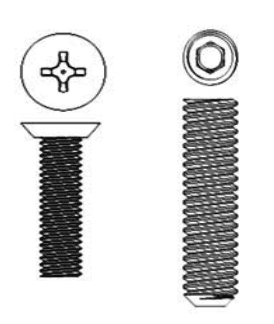
SCREW PACK 8
1-3/8” Adjustment Screw with 10-32 Internal Thread for Right Hand with 10-32 x 3/4” Flat Head Machine Screw
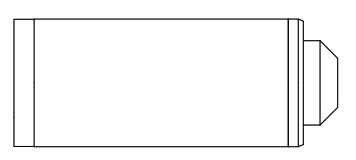
DRILL TOOL
Lorem Ipsum Lorem Ipsum
What Elements Make Stainless Steel “Stainless”?
Stainless steel is the term for grades of steel that contain more than 10% chromium, with or without other alloying elements. Stainless steel resists corrosion, maintains its strength at high temperatures, and is easily maintained. For these reasons, it is used widely in architectural hardware, chemical plants and highly corrosive atmospheres. The most common grades of stainless steel are type 304, The most commonly specified austenitic (chromium-nickel stainless class) stainless steel, accounting for more than half of the stainless steel produced in the world. This grade withstands ordinary corrosion, is durable in typical food processing environments, and resists most chemicals. Type 304 is available in virtually all product forms and finishes. Type 316 Austenitic (chromium-nickel stainless class) stainless steel containing 2%-3% molybdenum (whereas 304 has none). The inclusion of molybdenum gives 316 greater resistances to various forms of deterioration.
Unprotected carbon steel rusts readily when exposed to today’s atmospheric conditions of air and moisture. This iron oxide film (the rust) is active and accelerates corrosion by forming more iron oxide. The corrosion will continue until all the carbon steel is converted into iron oxide and because stainless steel contains at least 10% chromium, the oxidation of the iron is changed to produce a complex oxide that resists further oxidation and forms a passive layer on the surface.
The passive layer is only a few microns in thickness and will reform if it is removed by scratching or machining. If stainless steel is properly selected and maintained, it should not suffer any corrosion. For highly corrosive areas, 316 grade or PVD over 304L may be recommended. PBB’s standard grade stainless steel is 304L.
What Makes Stainless Steel Corrode?
Stainless steel is corrosion resistant and not corrosion proof and will corrode under certain conditions. Corrosion in stainless steel is not the same type of corrosion as found in carbon steel. The most likely form of stainless steel corrosion is “pitting”. Pitting occurs when the environment overpowers the ability of stainless steel to reform the passive layer. Normally dark brown pits occur on the surface of the stainless steel.
The three key types of corrosion that normally effect door hardware products are:
1. Atmospheric Corrosion – Atmospheric corrosion occurs when stainless steel is exposed to airborne liquids, solids or gases. Some sources of atmospheric corrosion are sea spray, rain in coastal zones, salt (possibly from de-icing), and dirt. This form of corrosion is typically worse outdoors, especially near marine environments.
2. Chemical Corrosion – Chemical corrosion takes place when stainless steel comes in direct contact with a material that has a high chloride concentration or a strong corrosive solution. Some factors which affect the severity of chemical corrosion include: chemical/chloride concentration level, duration of contact, frequency of washing, and the operating environment.
3. Contact Corrosion – A small piece of carbon steel, scale, copper, or foreign material lodged in stainless steel may be sufficient to destroy passivity at the point of contact and cause pitting. Carbon steel brushes and steel wool should never be used to clean stainless steel.
Stainless Steel – Magnetic Properties
In the metallurgy structure of stainless, the material creates and produces two conditions, first, almost all stainless material to be formed must be annealed to be soften enough for machining, second, when machining stainless the material becomes work hardened. With this many stainless steels can become magnetized.
In general, annealed 200 and 300 series stainless steels are nonmagnetic and cannot be magnetized in their natural state. These alloys become magnetic after severe cold working. All of the 400 series alloys are ferromagnetic and can easily become magnetized. The strength of the residual magnetism is controlled by many factors, including composition and heat treatment. In general, the harder the alloy, the stronger will be its remnant magnetism. All of the precipitation hardenable stainless steels are magnetic in the hardened condition.
Cold Working – Many cold drawn and/or polished stock have a noticeable amount of magnetism as a result of the previous cold work. This is particularly the case with grades 304 and 303, and much less so for the higher nickel grades such as 310 and 316. Even within the chemical limitations of a single standard analysis range there can be a pronounced variation in the rate of inducement of magnetic response from cold work.
Maintenance of Stainless Steel Finishes
Cleanliness is essential for maximum resistance to corrosion. Surface contamination by dirt or other materials hinders the ability of stainless steel to reform the passive layer and traps corrosive agents, reducing corrosion protection. In many cases, standard household cleaners can be used to clean and maintain stainless steel hardware items. Soap, ammonia, and detergent and water are used to clean normal dirt. Cleaning should always be followed by rinsing with clean water. When water contains mineral solids, which leave water spots, it is advisable to wipe the surface completely with dry towels.
In selecting cleaning practices, consider the possibility of scratching and the potential for post cleaning corrosion caused by incompletely removed cleaners. Select only cleaners that are not abrasive, not acidic, and low in chloride. Many antibacterial cleaners used to clean and sanitize door hardware contain high levels of chlorides, which will cause corrosion if not properly removed from the surface by rinsing. Routine cleaning is essential, especially in environments that have elevated levels of atmospheric corrosion. Proper care for your stainless steel door hardware will result in many years of durable use.
Acknowledgements:
Stainless Steel Industry of North America
ASM International – American Society of Metals
Euro Inox – European Stainless Steel Development Association
Still have questions?
Can’t find the answer you’re looking for? Chat with our team!